Key Takeaways
- O-rings are essential for preventing leaks and maintaining the integrity of automotive systems, enhancing vehicle safety and efficiency.
- Recent advancements in materials, such as high-performance elastomers and thermoplastic elastomers, allow O-rings to withstand extreme temperatures and pressures.
- Precision molding and 3D printing technologies have improved O-ring manufacturing, resulting in better durability and custom designs for specific applications.
- The rise of electric and hybrid vehicles has driven the development of multi-functional O-rings that meet unique sealing challenges, such as thermal management and electrical insulation.
- Investing in research and development is crucial for manufacturers to create scalable production methods and innovative materials that align with market demands.
- Sustainability is becoming a priority, with eco-friendly O-ring materials being developed to reduce environmental impact while maintaining performance.
- Collaboration between manufacturers and material scientists is key to overcoming technical challenges and advancing O-ring technology in the automotive industry.
Key Innovations in O-Ring Technologies
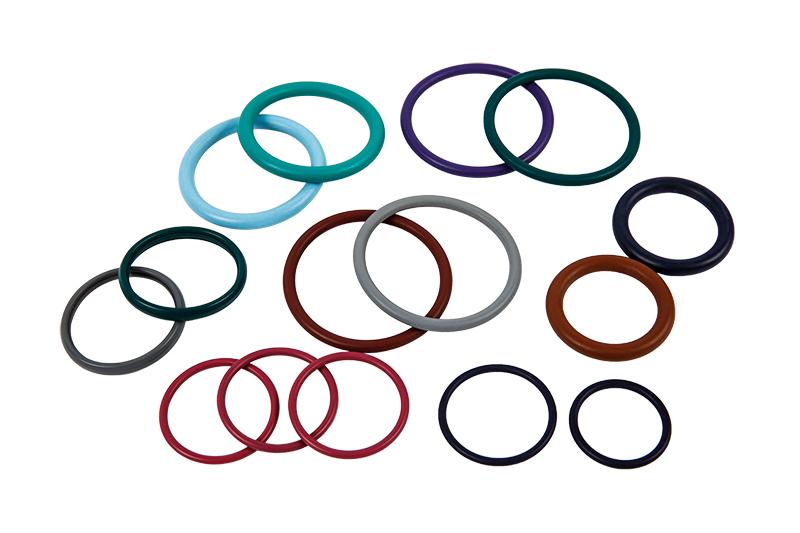
Advancements in O-Ring Materials
Development of high-performance elastomers for extreme temperatures and pressures.
The evolution of material science has significantly enhanced the capabilities of O-rings. High-performance elastomers, such as fluorocarbon and perfluoroelastomer compounds, now offer exceptional resistance to extreme temperatures and pressures. These materials maintain their elasticity and sealing properties even in harsh environments, such as turbocharged engines or high-pressure fuel systems. This advancement ensures that O-rings can perform reliably under conditions that would have previously caused material degradation or failure.
Thermoplastic elastomers (TPEs) represent another breakthrough in O-ring materials. Combining the flexibility of rubber with the processing efficiency of plastics, TPEs provide a versatile and sustainable option for modern automotive applications. Their recyclability and lower environmental impact align with the industry’s growing focus on eco-friendly solutions.
Use of chemical-resistant materials for fuel and oil systems.
Chemical exposure poses a significant challenge in automotive systems, particularly in fuel and oil applications. Modern O-rings utilize advanced chemical-resistant materials, such as hydrogenated nitrile butadiene rubber (HNBR) and ethylene propylene diene monomer (EPDM). These compounds resist swelling, cracking, and degradation when exposed to aggressive chemicals, including ethanol-blended fuels and synthetic oils. By ensuring long-term durability, these materials reduce maintenance needs and enhance the reliability of critical automotive systems.
Innovations in Manufacturing Processes
Precision molding techniques for enhanced durability and fit.
Manufacturing advancements have revolutionized the production of O-rings, improving both their quality and performance. Precision molding techniques now allow manufacturers to create O-rings with tighter tolerances and more consistent dimensions. This precision ensures a better fit, reducing the risk of leaks and enhancing the overall durability of the seal. These techniques also minimize material waste, contributing to cost efficiency and sustainability in production.
Adoption of 3D printing for custom O-ring designs.
The adoption of 3D printing technology has opened new possibilities for custom O-ring designs. This innovative approach enables the rapid prototyping and production of O-rings tailored to specific applications. For instance, engineers can design O-rings with unique geometries or material compositions to address specialized sealing challenges in electric vehicles or autonomous systems. By streamlining the development process, 3D printing accelerates innovation and reduces time-to-market for advanced sealing solutions.
Cutting-Edge O-Ring Designs
Multi-functional O-rings for hybrid and electric vehicles.
The rise of hybrid and electric vehicles (EVs) has driven the demand for multi-functional O-rings. These advanced designs integrate additional features, such as thermal insulation or electrical conductivity, to meet the unique requirements of EV systems. For example, O-rings used in battery cooling systems must provide effective sealing while also managing heat transfer. Such innovations ensure optimal performance and safety in next-generation vehicles.
Enhanced sealing technologies for improved efficiency.
Enhanced sealing technologies have redefined the efficiency of O-rings in automotive applications. Dual-seal designs, for instance, offer superior protection against leaks by incorporating multiple sealing surfaces. Additionally, self-lubricating O-rings reduce friction during operation, minimizing wear and extending service life. These advancements not only improve system efficiency but also lower maintenance costs, delivering greater value to end users.
Applications of Advanced O-Rings in Modern Vehicles
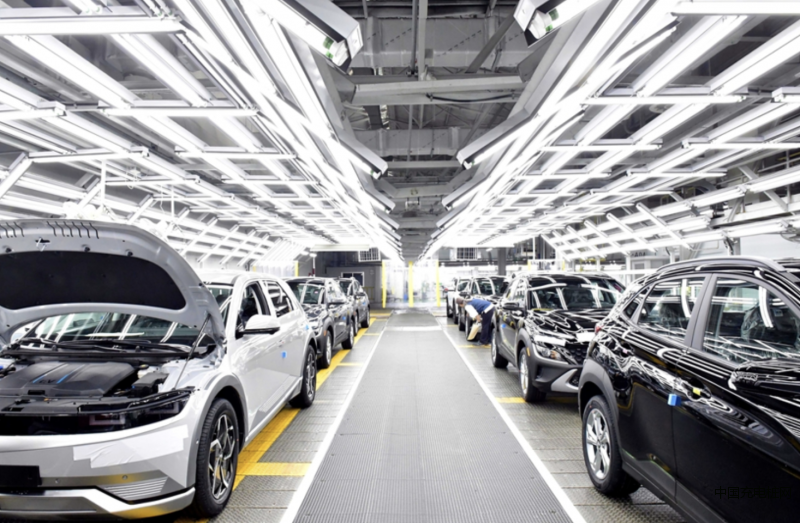
O-Rings in Internal Combustion Engines
Improved sealing in high-pressure fuel injection systems.
High-pressure fuel injection systems demand precision and reliability to ensure optimal engine performance. Advanced O-rings, crafted from innovative materials like fluorocarbon and hydrogenated nitrile butadiene rubber (HNBR), provide exceptional sealing capabilities under extreme pressures. These materials resist chemical degradation caused by ethanol-blended fuels and synthetic oils, ensuring long-term durability. By preventing fuel leaks, these O-rings enhance combustion efficiency and reduce emissions, aligning with stricter environmental regulations.
Enhanced durability in turbocharged engines.
Turbocharged engines operate under elevated temperatures and pressures, which can challenge traditional sealing solutions. Modern O-rings, such as those made from ACM (Acrylate Rubber), excel in these demanding conditions. Their heat resistance and ability to withstand exposure to oils and greases make them indispensable for turbocharged systems. These O-rings maintain their integrity over extended periods, reducing the risk of seal failure and minimizing maintenance costs for vehicle owners.
Role of O-Rings in Electric Vehicles (EVs)
Sealing solutions for battery cooling systems.
Electric vehicles rely heavily on efficient thermal management to maintain battery performance and safety. O-rings play a critical role in sealing battery cooling systems, preventing coolant leaks that could compromise the system’s efficiency. PFAS-free O-rings, made from advanced elastomers, have emerged as a sustainable choice for EV manufacturers. These O-rings withstand high temperatures and chemical exposure, ensuring reliable operation in challenging environments. Their eco-friendly composition also supports the automotive industry’s shift toward greener technologies.
Use in high-voltage electrical components.
High-voltage electrical components in EVs require robust sealing solutions to ensure safety and functionality. O-rings designed for these applications offer excellent insulation properties and resistance to electrical arcing. Silicone-based O-rings, known for their flexibility and thermal stability, are commonly used in connectors and powertrain systems. By providing secure seals, these O-rings protect sensitive components from moisture and contaminants, enhancing the overall reliability of electric vehicles.
Applications in Autonomous and Connected Vehicles
Ensuring reliability in advanced sensor systems.
Autonomous and connected vehicles rely on a network of sensors to navigate and communicate effectively. O-rings ensure the reliability of these sensors by providing airtight seals that protect against dust, moisture, and temperature fluctuations. Micro O-rings, specifically designed for compact sensor assemblies, maintain their sealing properties even after repeated compressions. This resilience ensures consistent sensor performance, which is critical for the safety and functionality of autonomous systems.
Sealing for electronic control units (ECUs).
Electronic control units (ECUs) serve as the brain of modern vehicles, managing various functions from engine performance to connectivity features. O-rings safeguard these units by sealing their enclosures against environmental factors such as water and dust. ECO (Epichlorohydrin) O-rings, with their resistance to fuels, oils, and ozone, are particularly suited for ECU applications. By protecting these vital components, O-rings contribute to the longevity and reliability of autonomous and connected vehicles.
Market Trends and Future Outlook
Growth of the Automotive O-Ring Market
Market data on the increasing demand for advanced sealing solutions.
The automotive O-ring market is experiencing robust growth, driven by the rising demand for advanced sealing solutions. The global market for automotive distributor O-rings, for instance, was valued at USD 100 million in 2023 and is projected to reach USD 147.7 million by 2031, growing at a 5% compound annual growth rate (CAGR) from 2024 to 2031. This growth reflects the increasing adoption of high-performance O-rings in modern vehicles, where precision and durability are critical.
North America, a key player in the automotive sector, is also witnessing significant expansion. The region’s automotive industry is expected to grow at a CAGR of over 4% in the next five years, further fueling the demand for innovative O-ring technologies. The global O-ring market, as a whole, is estimated to grow at a healthy CAGR of 4.2% over the same period, underscoring the importance of these components in the evolving automotive landscape.
Impact of EV and hybrid vehicle adoption on O-ring innovation.
The shift toward electric vehicles (EVs) and hybrid models has profoundly influenced O-ring innovation. These vehicles require specialized sealing solutions to address unique challenges, such as thermal management in battery systems and insulation for high-voltage components. The growing adoption of EVs has accelerated the development of advanced materials and designs tailored to these applications.
For example, PFAS-free elastomers have emerged as a sustainable choice for EV manufacturers, offering superior chemical resistance and thermal stability. Multi-functional O-rings, which integrate features like electrical conductivity, are also gaining traction in hybrid and electric vehicles. As the EV market expands, these innovations will play a pivotal role in enhancing vehicle performance and safety.
Future Directions in O-Ring Technology
Integration of smart materials for real-time monitoring.
The integration of smart materials represents a transformative trend in O-ring technology. These materials enable real-time monitoring of system conditions, such as pressure, temperature, and chemical exposure. By embedding sensors within O-rings, manufacturers can provide predictive maintenance solutions that enhance reliability and reduce downtime.
For instance, smart O-rings could alert users to potential leaks or material degradation before they lead to system failures. This proactive approach aligns with the automotive industry’s push toward connected and autonomous vehicles, where real-time data plays a crucial role in ensuring safety and efficiency. The adoption of such intelligent sealing solutions is expected to redefine the role of O-rings in modern vehicles.
Development of sustainable and eco-friendly O-ring materials.
Sustainability has become a central focus in the automotive industry, driving the development of eco-friendly O-ring materials. Manufacturers are exploring alternatives like thermoplastic elastomers (TPEs), which combine durability with recyclability. These materials reduce environmental impact while maintaining high performance under demanding conditions.
The use of bio-based elastomers is another promising avenue. Derived from renewable resources, these materials offer a sustainable solution without compromising on quality. As regulatory pressures and consumer preferences shift toward greener technologies, the adoption of sustainable O-ring materials will likely accelerate. This trend not only supports environmental goals but also positions manufacturers as leaders in innovation and corporate responsibility.
“The future of O-ring technology lies in its ability to adapt to changing industry demands, from sustainability to smart functionality, ensuring its continued relevance in the automotive sector.”
Advanced O-ring technologies have redefined the auto parts industry, driving significant improvements in vehicle performance, efficiency, and sustainability. By leveraging innovations in materials like thermoplastic elastomers and adopting cutting-edge manufacturing processes, manufacturers have enhanced product reliability while reducing environmental impact. These advancements not only address the demands of modern vehicles, such as electric and autonomous systems, but also pave the way for future breakthroughs. As automotive trends evolve, O-ring technology holds immense potential to further revolutionize sealing solutions, ensuring vehicles remain efficient, durable, and eco-friendly.
Post time: Dec-09-2024